Определить срок эксплуатации механического резца, выданного предприятием, важно для планирования ремонтных работ и замены оборудования. Однако, установить точный срок эксплуатации может быть непросто, так как он зависит от множества факторов, включая качество резца, режим работы и условия эксплуатации. В данной статье рассмотрим основные параметры, по которым можно приблизительно определить срок службы механического резца.
Влияние угла затачивания на силу резания
Принцип угла затачивания заключается в том, что при неправильном выборе угла затачивания возникает большая сила резания, что приводит к повышенному износу и преждевременному износу механического резца. Наоборот, при правильно подобранном угле затачивания сила резания снижается, что позволяет достичь более эффективной резки.
Оптимальные значения угла затачивания
Для разных материалов оптимальные значения угла затачивания могут различаться. В таблице ниже приведены рекомендуемые значения угла затачивания для некоторых материалов:
Материал | Угол затачивания |
---|---|
Сталь | 5-10 градусов |
Алюминий | 30-45 градусов |
Пластик | 60-90 градусов |
Плюсы и минусы разных углов затачивания
- Угол затачивания 0 градусов. При таком угле затачивания сила резания будет минимальной, но качество обработки будет низким, так как будет образовываться большое количество стружки.
- Угол затачивания 30 градусов. Этот угол подходит для обработки большинства материалов. Сила резания будет средней, а качество обработки – достаточно высоким.
- Угол затачивания 60 градусов. При таком угле затачивания сила резания будет высокой, но качество обработки будет низким, так как будут образовываться мелкие стружки.
Правильный выбор угла затачивания является важным фактором для снижения силы резания при использовании механического резца. Рекомендуется учитывать особенности материала и выбирать оптимальный угол затачивания, чтобы достичь более эффективной резки и повысить срок службы инструмента.
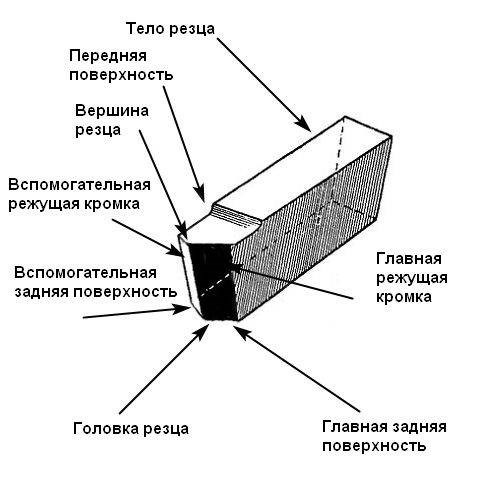
1. Область применения механического резца
1.1 Производство
Механические резцы используются в промышленности для резки металлов, пластмасс, стекла и других материалов. Они позволяют осуществлять точную и качественную резку для производства различных изделий и деталей.
1.2 Строительство
В строительной отрасли механические резцы применяются для резки кирпича, бетона, камня и других строительных материалов. Они позволяют мастерам точно выполнять необходимые размеры и формы для установки различных конструкций и элементов.
1.3 Ремонт и обслуживание
Механические резцы широко используются в ремонтных и обслуживающих работах. Они позволяют производить резку и удаление поврежденных или изношенных деталей, а также выполнять монтаж и сборку новых компонентов.
1.4 Ручное творчество
Механический резец может быть полезным инструментом для ручного творчества и хобби. Он позволяет создавать декоративные элементы из различных материалов, таких как дерево, пластик, кожа и т. д.
В целом, область применения механического резца очень широка и охватывает множество отраслей и сфер деятельности. Он является незаменимым инструментом для профессионалов и любителей, позволяющим быстро и точно выполнять различные работы, связанные с резкой и разделкой материалов.
Технические требования к сроку эксплуатации механического резца
Срок эксплуатации механического резца, который был предоставлен предприятием, определяется рядом технических требований, которым должен соответствовать этот инструмент. Ниже перечислены три основных требования, которые должны быть учтены при использовании механического резца.
1. Качество материалов
Срок эксплуатации механического резца прямо зависит от качества материалов, используемых при его изготовлении. Основные компоненты резца, такие как лезвия и ручки, должны быть выполнены из высококачественных материалов, обладающих необходимой прочностью и износостойкостью. Для достижения долгого срока службы резца, желательно использовать инструменты, изготовленные из стали с высоким содержанием углерода или из сплавов с применением термической обработки.
2. Точность изготовления
Точность изготовления механического резца также играет важную роль в его сроке эксплуатации. Режущие кромки лезвий должны быть правильно заточены и иметь оптимальный угол заточки. Ручки резца должны быть удобными для использования и надежно закреплены, чтобы предотвратить их отваление или поломку. При выборе механического резца следует обратить внимание на качество его изготовления, чтобы убедиться в его долговечности и надежности.
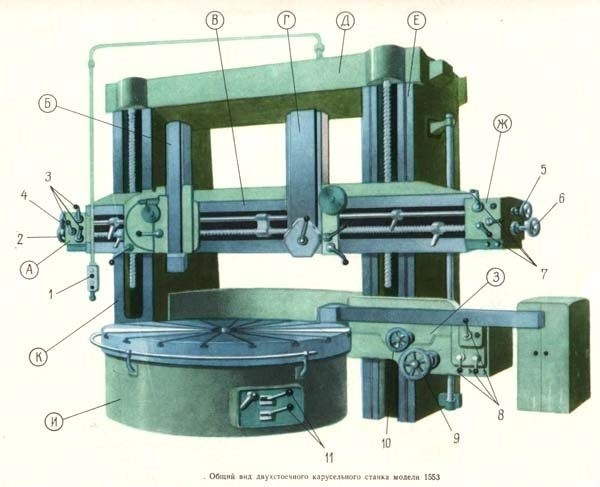
3. Правильное использование и уход
Даже при соответствии механического резца указанным выше техническим требованиям, его срок службы может быть заметно сокращен, если инструмент не используется правильно или не подвергается необходимому уходу. Важно следовать инструкциям по эксплуатации, не превышать нагрузку, на которую рассчитан резец, и регулярно проводить мойку и смазку инструмента. Также рекомендуется хранить резец в специальных защитных кейсах или подвесках, чтобы предотвратить его повреждение во время хранения или транспортировки.
Соблюдение указанных выше технических требований поможет максимизировать срок эксплуатации механического резца, предоставленного предприятием. Качество материалов, точность изготовления и правильное использование и уход — основные аспекты, которые следует учитывать при выборе и использовании этого инструмента.
Износ резца по передней (а) и задней (б) поверхностям резца
Износ передней (а) поверхности резца
Передняя (а) поверхность резца является рабочей частью, контактирующей с обрабатываемым материалом. Износ данной поверхности может быть вызван следующими факторами:
- Абразивность материала: Если обрабатываемый материал является абразивным, то это может привести к быстрому износу передней (а) поверхности резца.
- Температурный износ: При обработке материала может возникать высокая температура, которая может вызвать плавление или размягчение передней (а) поверхности резца и привести к ее быстрому износу.
- Механическое воздействие: При обработке материала может происходить механическое воздействие, такое как удары или трение, что также может привести к быстрому износу передней (а) поверхности резца.
Износ задней (б) поверхности резца
Задняя (б) поверхность резца является поддерживающей поверхностью и обычно не контактирует с обрабатываемым материалом. Однако, износ данной поверхности также может быть проблемой в производственном процессе. Возможные причины износа задней (б) поверхности резца:
- Фрикционный износ: При взаимодействии резца с другими поверхностями, такими как крепежные элементы или крепежные устройства, может происходить фрикционный износ, который приводит к износу задней (б) поверхности резца.
- Термический износ: При обработке материала может быть создана высокая температура, которая может вызывать термический износ задней (б) поверхности резца.
Износ резца по передней (а) и задней (б) поверхностям может негативно влиять на его производительность и эффективность. Поэтому предприятию необходимо регулярно контролировать износ резца и принимать меры по его замене или восстановлению.
Инструмент для заточки резцов
Инструменты для заточки резцов
- Заточной станок. Это специализированное устройство, которое обеспечивает точную и стабильную заточку резцов. Существуют различные модели заточных станков, включая ручные и автоматические.
- Шлифовальные камни. Они используются для шлифовки и полировки режущей кромки резца. Камни могут быть разной формы и зернистости, в зависимости от типа резца и требуемого качества заточки.
- Разметочный инструмент. Это инструмент, который позволяет проводить точные разметки на резце перед его заточкой. Разметка помогает сориентироваться при заточке и достичь необходимых параметров режущей кромки.
Методы заточки резцов
1. Ручная заточка. Этот метод подразумевает заточку резца вручную с использованием заточных камней и разметочного инструмента. Ручная заточка требует определенных навыков и опыта, чтобы достичь точности и качества заточки.
2. Автоматическая заточка. Этот метод осуществляется при помощи специальных заточных станков, которые обеспечивают автоматическую и точную заточку резцов. Автоматическая заточка может быть более быстрой и эффективной, поскольку она исключает человеческий фактор.
Техники заточки резцов
- Подготовка резца. Перед заточкой резец должен быть тщательно очищен от загрязнений и остатков материала. Это позволяет получить более точную и качественную заточку.
- Разметка резца. Прежде чем приступить к заточке, необходимо провести разметку на резце. Разметка определяет углы и параметры заточки, а также помогает сориентироваться при процессе заточки.
- Заточка режущей кромки. Необходимо последовательно провести шлифовку и полировку режущей кромки резца с использованием шлифовальных камней. Это позволяет достичь необходимой остроты и гладкости режущей кромки.
- Проверка качества заточки. После завершения заточки необходимо проверить качество и точность заточенной режущей кромки. При необходимости можно повторить процесс заточки для достижения требуемых параметров.
Цитата
Заточка резцов — важный процесс, который позволяет продлить срок службы механического резца и обеспечить качественную обработку материала. Правильный выбор инструмента, метода и техники заточки является основополагающим для достижения желаемых результатов.
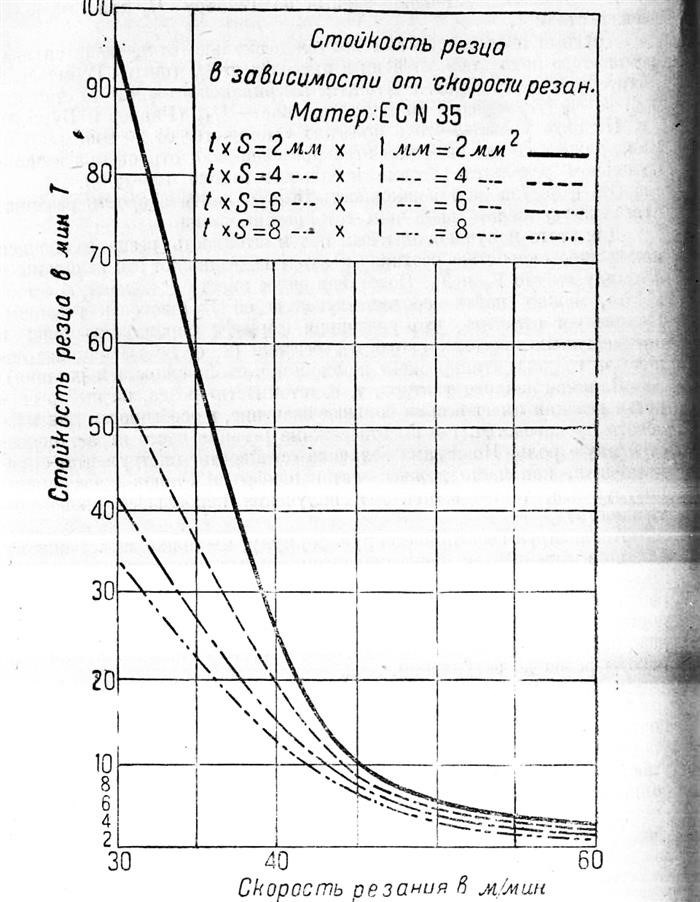
Использование правильных инструментов, методов и техник заточки резцов позволяет не только восстановить остроту и работоспособность инструмента, но и продлить его срок службы. Регулярная заточка резцов является неотъемлемой частью процесса обработки материала и играет важную роль в обеспечении качества производства.
Как маркируют пластины, и кто их производит
Одним из важных производителей пластин является предприятие «Альфа». Компания использует самые передовые технологии для создания высококачественных металлических и пластиковых пластин, которые имеют широкий спектр применения в различных отраслях промышленности.
Методы маркировки пластин:
- Гравировка — это процесс нанесения кодов на поверхность пластины с помощью режущего инструмента. Этот метод позволяет создавать прочные и долговечные метки, которые нельзя стереть.
- Лазерная маркировка — технология, основанная на использовании лазерного луча для создания меток на поверхности пластины. Этот метод обеспечивает большую точность и высокую скорость маркировки.
- Термоэлектрическая маркировка — процесс нанесения кодов с помощью высокотемпературного инструмента. Этот метод позволяет создавать яркие и четкие метки.
Информация на маркировке:
На маркировке пластин указывается следующая информация:
- Название производителя — это имя компании, которая изготовила пластину. Это позволяет идентифицировать производителя и установить его ответственность за качество продукции.
- Характеристики пластины — это информация о материале, размерах, форме и других технических характеристиках пластины. Это помогает пользователям выбрать правильную пластину для своих нужд.
- Дата производства — это дата, когда пластина была изготовлена. Эта информация позволяет контролировать срок годности пластин и предотвращает использование устаревшей продукции.
- Срок эксплуатации — это период времени, в течение которого пластина может быть безопасно использована. Эта информация важна для безопасности и эффективности использования пластин.
Преимущества маркировки пластин:
Маркировка пластин имеет ряд преимуществ:
- Идентификация — маркировка позволяет идентифицировать и отличать пластины от других изделий.
- Контроль качества — маркировка позволяет установить происхождение и производителя пластин, что помогает контролировать качество продукции.
- Безопасность — информация о сроке эксплуатации помогает проверять состояние пластин и предотвращает использование просроченных изделий.
- Выбор — информация о характеристиках пластин помогает пользователям выбрать правильный продукт для своих нужд.
Керамические пластины: особенности применения в точении
Основные преимущества керамических пластин в точении:
- Высокая твердость и износостойкость. Керамические пластины имеют высокую твердость и способны выдерживать большие нагрузки.
- Низкое трение и теплопроводность. Благодаря этому свойству, керамические пластины позволяют снизить трение между режущим инструментом и обрабатываемым материалом, что увеличивает срок службы резца.
- Устойчивость к высоким температурам. Керамика не изменяет своих свойств при высоких температурах, что позволяет использовать пластины в процессе точения при высоких скоростях.
- Хорошая антиадгезионная способность. Это свойство керамических пластин позволяет предотвратить прилипание стружки к режущему инструменту и улучшить качество обработки.
- Химическая стойкость. Керамические пластины устойчивы к воздействию агрессивных химических сред, что позволяет использовать их в широком диапазоне промышленных отраслей.
Применение керамических пластин в точении:
За счет своих уникальных свойств, керамические пластины находят применение в различных процессах точения металлов. Они способны обрабатывать как обычные, так и твердые и износостойкие материалы.
Материал | Применение керамических пластин |
---|---|
Сталь | Точение стальных деталей с высокой твердостью и прочностью. |
Чугун | Обработка чугунных деталей с высокой твердостью и износостойкостью. |
Алюминий | Точение алюминиевых деталей с высокой точностью и качеством. |
Керамические пластины не только улучшают качество обработки и увеличивают срок службы резца, но и позволяют сократить время и затраты на процесс точения. Это делает их незаменимыми инструментами в промышленном производстве.
Использование керамических пластин в точении – эффективное решение для достижения высокой точности и качества обработки металлических деталей.
Таблица углов заточки
Ниже приведена таблица углов заточки для различных типов материалов:
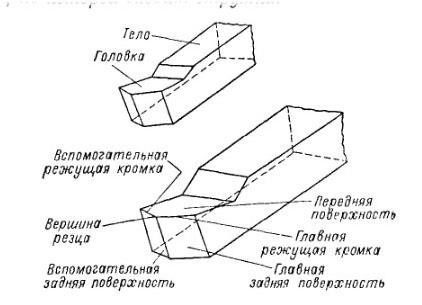
Тип материала | Угол заточки | Примечание |
---|---|---|
Сталь | 40-60 градусов | Рекомендуется использовать угол 45 градусов для общего использования |
Алюминий | 60-90 градусов | Угол заточки зависит от конкретного типа алюминия и его сплавов |
Пластик | 30-45 градусов | Рекомендуется использовать угол 30 градусов для лучшей производительности |
Дерево | 25-40 градусов | Угол заточки зависит от типа дерева и требуемого качества поверхности после резки |
Важно помнить, что эти значения являются рекомендованными и могут меняться в зависимости от конкретных условий использования и требований. При заточке резца необходимо учитывать также другие факторы, такие как тип заземления резца и качество заточки его режущей кромки.
Соблюдение оптимальных углов заточки позволит достичь оптимальной производительности и увеличить срок эксплуатации механического резца.
Когда нужно затачивать резец
Признаки нужды в заточке
- Повреждения режущей кромки. Если на режущей кромке резца появились зазубрины, сколы или трещины, это является явным признаком того, что резец нуждается в заточке. Такие повреждения могут возникнуть из-за неправильного использования или износа режущей кромки.
- Потеря точности резания. Если резец перестал обеспечивать нужную точность при обработке материала, это может быть связано с тем, что его режущая кромка потеряла остроту. В этом случае, затачивание резца позволит восстановить его работоспособность и вернуть точность резания.
- Снижение производительности. Если при работе с резцом производительность снижается, скорее всего, это связано с тем, что его режущая кромка уже не способна эффективно справляться с задачей. Заточка резца поможет восстановить его работоспособность и повысить производительность.
Регулярность заточки
Чтобы поддерживать резец в работоспособном состоянии, необходимо регулярно производить его заточку. Частота заточки может зависеть от условий эксплуатации резца и конкретного производства. Однако, в среднем, механический резец рекомендуется заточить каждые 2-4 недели.
Кроме того, необходимо учитывать такие факторы, как материалы, с которыми работает резец, и интенсивность его использования. Если резец работает с твердыми или абразивными материалами, он может требовать более частой заточки. Также, если резец используется в режиме непрерывной или интенсивной работы, регулярная заточка может быть необходима чаще.
Заточка механического резца играет важную роль в его долговечности и эффективном использовании. Поэтому, важно вовремя определять признаки необходимости заточки, такие как повреждения режущей кромки, потеря точности резания и снижение производительности. Регулярная заточка резца позволит поддерживать его в работоспособном состоянии и обеспечивать высокую эффективность производства.
2 Нормативные ссылки
2.1 Нормативные документы на механические резцы
- ГОСТ 18876-73 «Инструмент металлорежущий алмазный и абразивный. Образцы» — определяет образцы инструментов алмазных и абразивных для контроля и сравнения.
- ГОСТ 18877-73 «Инструмент металлорежущий алмазный и абразивный. Методы испытания» — устанавливает методы испытаний инструментов алмазных и абразивных для определения их технической характеристики.
- ГОСТ 18878-73 «Инструмент металлорежущий алмазный и абразивный. Технические условия» — содержит требования к конструкции и параметрам алмазных и абразивных инструментов.
2.2 Срок эксплуатации механического резца
Срок эксплуатации механического резца зависит от многих факторов, включая условия использования, качество материала резки и качество самого инструмента. Он также может быть указан в технических условиях или инструкции по эксплуатации.
Однако, следует отметить, что сам по себе механический резец является подверженным износу элементом и его срок службы может быть существенно сокращен в зависимости от интенсивности использования и правильности эксплуатации.
Керамические пластины для обработки жаропрочных суперсплавов: советы по применению
Выбор подходящего типа пластин
Перед началом работы необходимо выбрать подходящий тип керамических пластин в зависимости от материала, который будет обрабатываться. Разные жаропрочные суперсплавы требуют разных типов пластин, чтобы достичь оптимального качества обработки.
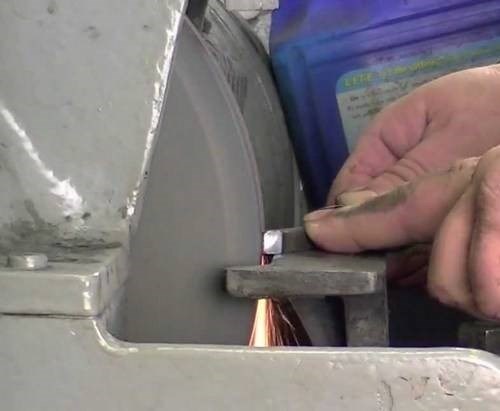
Правильная подготовка поверхности
Перед началом обработки необходимо правильно подготовить поверхность материала. Это включает удаление грязи, жира и других загрязнений с помощью специальных средств. Также рекомендуется убедиться, что поверхность суперсплава достаточно ровная.
Контроль скорости и нагрузки
Одним из ключевых аспектов обработки жаропрочных суперсплавов является правильное управление скоростью и нагрузкой на керамические пластины. Контролируя эти параметры, можно достичь наилучших результатов обработки и предотвратить износ пластин.
Использование специальных охлаждающих жидкостей
Суперсплавы обычно обрабатываются при высоких температурах, что может вызвать нагревание пластин и ухудшение их качества. Чтобы предотвратить это, рекомендуется использовать специальные охлаждающие жидкости, которые помогут снизить температуру и увеличить срок службы пластин.
Регулярное обслуживание и замена пластин
Для поддержания оптимальной производительности и качества обработки рекомендуется регулярно обслуживать и проверять состояние керамических пластин. При необходимости нужно производить замену изношенных пластин.
Следуя этим советам, можно добиться оптимальных результатов при обработке жаропрочных суперсплавов с помощью керамических пластин. Не забывайте о правильном выборе пластин, подготовке поверхности, контроле скорости и нагрузки, использовании охлаждающих жидкостей, а также регулярном обслуживании и замене пластин. Это поможет увеличить срок службы пластин и достичь высокого качества обработки суперсплавов.
Параметры классификации изделий
1. Функциональное назначение
Функциональное назначение – это основная задача, которую выполняет изделие. Оно определяет его основные характеристики и позволяет установить соответствие с требованиями потребителя. Важно четко определить функциональное назначение изделия, чтобы правильно выбрать его параметры и обеспечить эффективное функционирование.
2. Производственный материал
Производственный материал также является важным параметром классификации изделий. Он определяет надежность, долговечность и эксплуатационные характеристики изделия. Различные материалы могут иметь разные свойства и применение, поэтому правильный выбор производственного материала является ключевым для успешной эксплуатации изделия.
3. Габариты и размеры
Габариты и размеры изделия определяют его внешний вид, а также его совместимость с другими элементами. Важно учесть требования к габаритам и размерам, чтобы изделие было удобно в использовании и могло быть эффективно встроено в систему. Оптимальные габариты и размеры также позволяют снизить затраты на производство и транспортировку изделий.
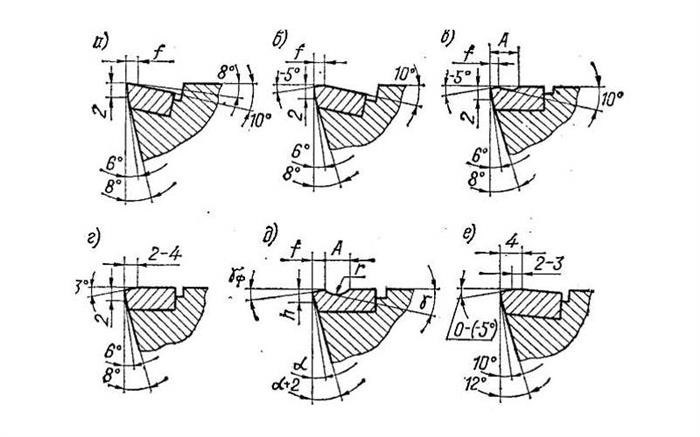
4. Технические характеристики
Технические характеристики изделия включают в себя такие параметры, как мощность, скорость, точность, надежность и другие. Они определяют функциональные возможности и производительность изделия. Правильный выбор технических характеристик позволяет достичь требуемых результатов при работе изделия и обеспечить его долговечность и надежность.
5. Стоимость и цена
Стоимость и цена изделия являются важными параметрами, которые влияют на его конкурентоспособность и доступность для потребителя. Оптимальная цена должна учитывать производственные затраты, налоги, маржу и спрос на рынке. Правильная оценка стоимости и цены позволяет достичь баланса между качеством изделия и его стоимостью для потребителя.
6. Экологические параметры
Экологические параметры включают в себя такие характеристики, как уровень шума, выбросы вредных веществ, энергопотребление и другие. Эти параметры определяют экологическую безопасность изделия и его влияние на окружающую среду. Важно учитывать экологические параметры при разработке и производстве изделия, чтобы минимизировать его негативное воздействие на окружающую среду.
7. Эргономические характеристики
Эргономические характеристики определяют удобство использования изделия для пользователя. Они включают в себя такие параметры, как удобная форма, удобные кнопки и рычаги, прочный и удобный материал для рукоятки и другие. Правильное учет эргономических характеристик позволяет создать комфортные условия работы с изделием и повысить его эффективность.
Правильная классификация изделий и учет всех параметров позволяет определить их основные характеристики и обеспечить их эффективную эксплуатацию. Оптимальный выбор параметров классификации помогает улучшить качество и надежность изделий, а также повысить их конкурентоспособность на рынке.